About Udupi Saree
The tradition of weaving in India is 4500 years old. In terms of the number of people it employed, it was second only to agriculture. Cloth made in the subcontinent was exported to other parts of the world. The advent of cloth made in the mills of Britain after the Industrial Revolution dealt a severe blow to the weavers of the subcontinent. Nonetheless, weaving has not only survived in India and Bangladesh, but many exquisite handloom products are still being made.
The subcontinent is one of the few parts of the world where weaving using handlooms still survives. The weaving of Udupi Sarees is one of the finest examples of this tradition giving a large number of skilled people employment opportunities locally in an eco-friendly industry.
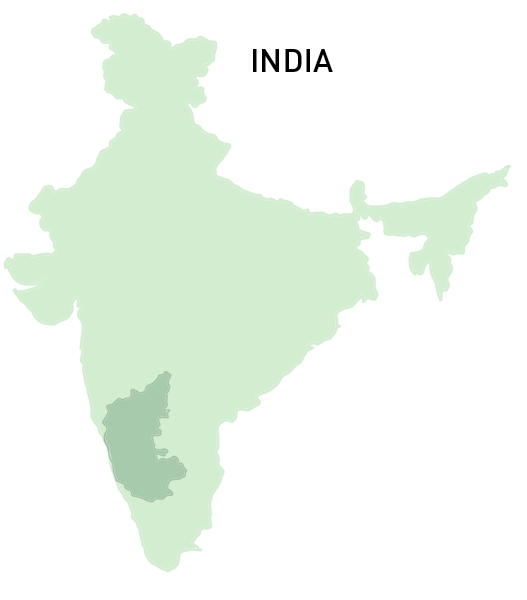
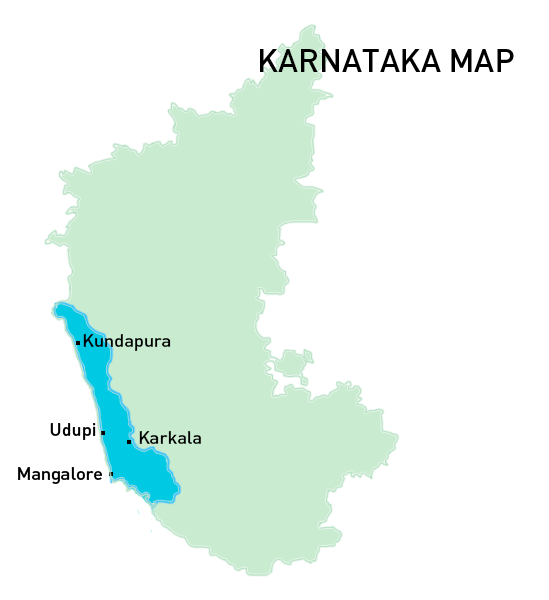
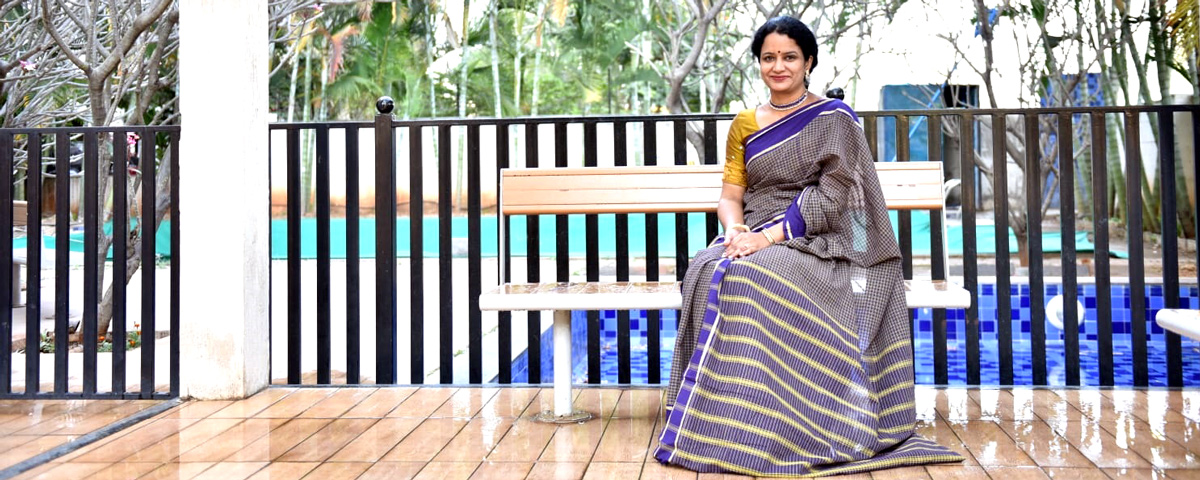
Udupi Sarees are woven in the geographical region of Dakshina Kannada and Udupi districts. Most of the weavers belong to the Padmashali(also called Shettigar) community.
The sarees are woven using fine 40, 60 and 80 count single-ply combed cotton yarns and have a very long life. Udupi sarees are woven on Malabar frame looms introduced by the Basel Mission in the nineteenth century. The Sarees have a plain or chequered design on the body with contrasting colour on the pallu and border. There are certain unique practices in the production of these sarees. The pallu portions of the warp are dyed in a dark shade after preparing the warp. A sizing of starch is applied to the warp on the loom using a brush at the time of weaving. A cut-border technique is employed to weave chequered sarees. Motifs are made
using the extra weft technique. These unique features are mentioned as salient features of the Udupi Sarees in the GI tag documentation dated 2016.
These delicate-looking but durable sarees last for generations. As they get older, they are used as bedspreads, soft baby wraps and kitchen towels before being returned to the soil from which they came. They have a negligible carbon footprint.
The Udupi Saree, having a history of more than two hundred years, flourished till about 1980. Udupi Sarees are produced at five weavers’ societies, namely Udupi, Shivalli, Brahmavara, Padupanamboorand Talipady, and under Karnataka Handloom Development Corporation (KHDC) .
Thereafter, especially post-liberalisation, its production saw a steady decline. It came close to extinction and a survey conducted by the Kadike trust in 2017 revealed that only forty-two weavers continued to make Udupi Sarees in the two districts.
It is in this grim situation that Kadike Trust started the Udupi Saree Revival programme in association with the Talipady Weavers’ Society.
As part of the revival effort, Brand Udupi Saree has been created with an attractive logo. Each saree is sold with a label carrying the logo and the name and picture of the weaver who made the saree.
By using social media to target buyers who appreciate the uniqueness of the Udupi Sarees, the sarees could be sold at a better price, the benefit of which is passed on to the weavers. Now the weavers are getting higher remuneration as well as recognition for their work. Exceptional weavers are felicitated on special occasions and their names are bieng referred to institutions for awards. As a result of these efforts, some weavers who had left the profession returned.
Further, new weavers are being trained by the Trust with financial assistance from the National Bank for Agriculture and Rural Development (NABARD). Young weavers are entering the profession for the first time in two decades. The number of weavers in Talipady Society increased from 8 to 34. Among the new weavers some are in their thirties who were trained by the Trust.There are now more than 70 weavers in the two districts.
Uniqueness of Udupi saree
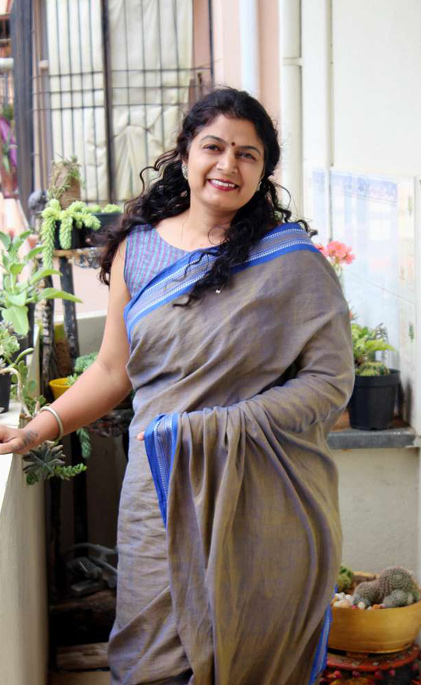
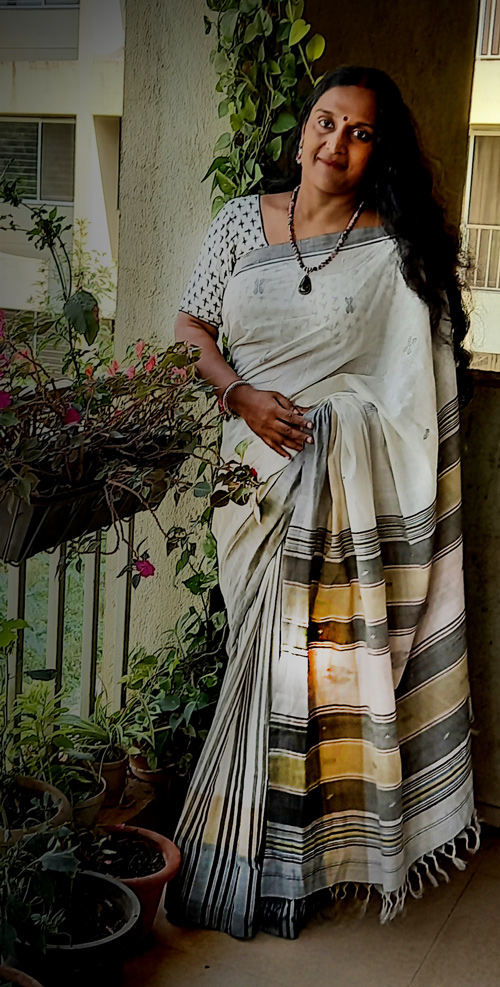
The Udupi saree is woven using the best quality single ply combed cotton yarns for both warp and weft. Sarees are woven using yarns in counts 120” ,100”, 80″, 60″ and 40” for both warp and weft. Now 100 and 120 counts are not used.
Artificial Zari or cotton yarns are used to create design in body, border and pallu portion using extra weft technique.
The saree has plain or checked design in the body and dobby or plain design in the border.
Light shades are used for the body, bright and contrast colours for the border and pallu.
The body of the saree is a simple plain weave. Extra warp patterns are woven on the border and pallu using dobby mechanism. In some sarees small butta (motifs) designs are created on the pallu and body of the saree with/without dobby mechanism using extra weft techniques.
Using pearl kind of lines known as warp rib weave on the pallu is another striking feature of Udupi Saree.
The yarns (used for the body of the saree) are dyed in desired colour before pre loom works (like bobbin winding) begins. The pallu portion of the saree yarns are dyed in dark shade after the warp stage (before weaving) using tie and dye technique. This gives bright contrast colour to the pallu portion.
Unique method of sizing known as ‘loom sizing’ practiced by Udupi saree weavers. The sizing material is applied directly to the yarn while the weaving is in progress.
A special brush with bristles made from the parts of ‘Fish tail Palm tree’ (Caryota urens) which is under threat now, is used to brush the yarn during the process of sizing. The sizing reduces the yarn breakage and improves the quality and efficiency of weaving. The on-loom sizing provides good stiffness and shining finishes to the woven Saree.
Natural materials such as fire wood and waste materials like coconut shells are used for scouring of yarn and preparation of dye bath etc. Hence there is very little pollution.
The looms used for weaving Udupi Sarees are frame looms known as Malabar Frame looms. Since the Missionaries of the German Basel Mission introduced the frame looms in the Malabar region, it is called Malabar Frame Looms.
The looms are equipped additionally with dobby and jacquard (optional). The dobby is used to produce extra warp design on the border of the saree. The Jacquard is used to weave designs with extra warp or extra weft or both (now not in use). Generally small and medium sized floral butta (motifs) designs are woven.
The other important and unique technique widely used in these districts is cut border technique for creating solid border for the Saree. In this technique, three shuttles are used. i.e. two shuttles for the borders and pallu and one shuttle for body portion. The cut border technique is used to weave bright contrast solid colour in border portion. Generally, checkered sarees are woven using cut border technique.